A Microlens Array (MLA) is an optical component composed of multiple tiny lenses arranged in a specific way, and is widely used in fields such as beam shaping, uniform illumination, 3D imaging, optical communication, and laser processing. Its processing technology and basic parameters directly affect the optical performance and application effect. The following is a detailed introduction:
Processing Technology of Microlens Arrays
The processing techniques for microlens arrays are diverse. The appropriate method should be selected based on factors such as material, precision requirements, and cost.
1. Lithography and ion etching methods
Features: High precision (sub-micron level), suitable for high-density arrays, but the equipment cost is high.
2. Hot-melt method
Features: Suitable for spherical lenses, simple process, but limited in shape.
3. Imprint/nanoimprint (NIL)
Features: Suitable for mass production, low cost, but the template making is complex.
4. Laser direct writing or femtosecond laser processing
Features: High flexibility, suitable for aspheric or freeform surfaces, but relatively low efficiency.
5. Injection molding
Features: Suitable for low-cost and large-scale production, but with high requirements for mold precision.
6. Gray-scale Lithography
Features: It can process aspheric surfaces without etching, but the mask design is complex.
Basic Parameters of Microlens Arrays
The performance of the microlens array is described by the following key parameters:
1. Geometric parameters
- Lens diameter: The diameter of a single lens, typically ranging from 10 μm to 1 mm.
- Focal Length: The focusing distance of a lens on parallel light, which is related to the radius of curvature and refractive index.
- Array period (Pitch) : The distance between the centers of adjacent lenses, affecting the fill factor.
- Fill Factor: The ratio of the effective optical area to the total area, with an ideal value of 100%.
- Surface Profile: Spherical, aspherical, cylindrical, etc., which affect the aberration correction ability.
2. Optical parameters
- Numerical Aperture (NA) : NA = n·sinθ (where n is the refractive index and θ is the receiving Angle), which determines the light collection capacity.
- Transmittance: The influence of materials (such as fused quartz, polymers) and coatings.
Wavefront Error: It characterizes optical quality and is usually required to be within λ/4 (where λ is the wavelength).
3. Material parameters
- Base materials: glass (high-temperature resistant, high transmittance), silicon (for infrared applications), polymer (low cost).
- Refractive index: Affects focal length and chromatic aberration (for example, the refractive index of PMMA is approximately 1.49@589nm).
4. Arrangement method
Hexagonal arrangement: High fill factor, suitable for uniform lighting.
- Square arrangement: Easy to align, but with a lower fill factor.
- Random arrangement: Reduces diffraction interference.
Requirements for Processes and Parameters of the application
1. Beam homogenization: High fill factor and low aberration are required.
2. 3D imaging (such as light field cameras) : Strict focal length consistency and low distortion are required.
3. Laser processing: High damage threshold materials (such as fused silica) are required.
Challenges and Development Trends
High-precision processing: nano-scale surface shape control.
Hybrid optical design: Enhancing performance by integrating diffractive optical elements (DOE).
Low cost: such as polymer imprinting technology.
By rationally selecting processes and parameter designs, microlens arrays can meet diverse optical requirements. In actual production, it is necessary to balance precision, cost and batch size.
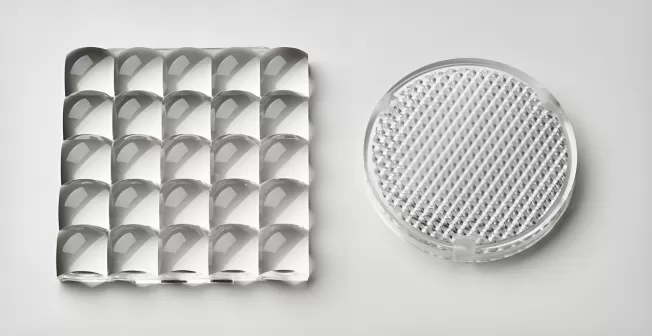