Customized optical components supplier to share with you:
The glass industry is a high energy consumption industry, and the glass melting furnace is the equipment with the most energy consumption of the glass production line, and the fuel cost accounts for about 35% to 50% of the glass cost. Most of the glass liquid consumption of float glass melting furnace designed by China can reach 6500kJ/kg ~ 7500kJ/kg, while only 5800kJ/kg of glass liquid can be consumed by large float glass enterprises abroad.
The thermal efficiency of glass kilns in developed countries is generally in the range of 30% ~ 40%, while that of Chinese glass kilns is only 25% ~ 35% on average.
Secondly, the backward operation technology and imperfect management of the domestic float glass process are also the causes of high energy consumption, poor melting quality, and short kiln life. Up to now, China has more than 140 float glass production lines, glass production capacity is increasing rapidly, and the market competition is heating up gradually.
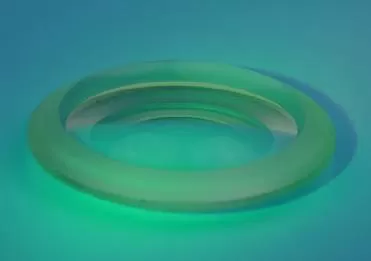
Double Concave Lens
As the main fuel of glass heavy oil, the price continues to go up, in the glass cost of an increasing proportion. Therefore, reducing glass energy consumption is of great significance for reducing production costs, improving the market competitiveness of enterprises, reducing environmental pollution and alleviating energy shortage.
The energy-saving of OEM optical components is a long-term task, and the technical personnel at home and abroad are actively studying, such as optimizing the structure design of kiln, oxygen-rich combustion, total oxygen-combustion electric fusion, heavy oil emulsion technology, etc. At present, many enterprises have started to implement energy-saving measures in the production process and explore energy-saving measures in glass production process control.
It is well known that the water content, temperature, and fuel consumption of the composite are closely related to the temperature of the composite. When the temperature of the mixture is greater than 35℃, most of the water adheres to the surface of refractory sand grains in the free state, so that more soda ash can be adhered to enhance the melting effect. When the temperature of the composite material is less than 35℃, the water in the composite material will form na2co3.10h2o or na2co3.7h2o with soda ash, and na2so4.10h2o crystalline water with glaub salt, so that the surface of the sand will lose water and become dry, and the melting function will be weakened.
Due to the low temperature in the northern region in winter, the temperature of the compound is generally lower than 35℃, and some areas even only about 20℃. In order to keep the appearance of the material wet, usually take the method of increasing the water of the material, although it plays a certain role, it will also bring more disadvantages, such as silo wall caking phenomenon, fuel consumption increase. Some people calculated that the amount of oil needed to enter the kiln was 0.085kg oil /kg water.